Unlocking Excellence in Metal Fabrication and Rapid Prototyping: A Comprehensive Guide for Innovative Manufacturing
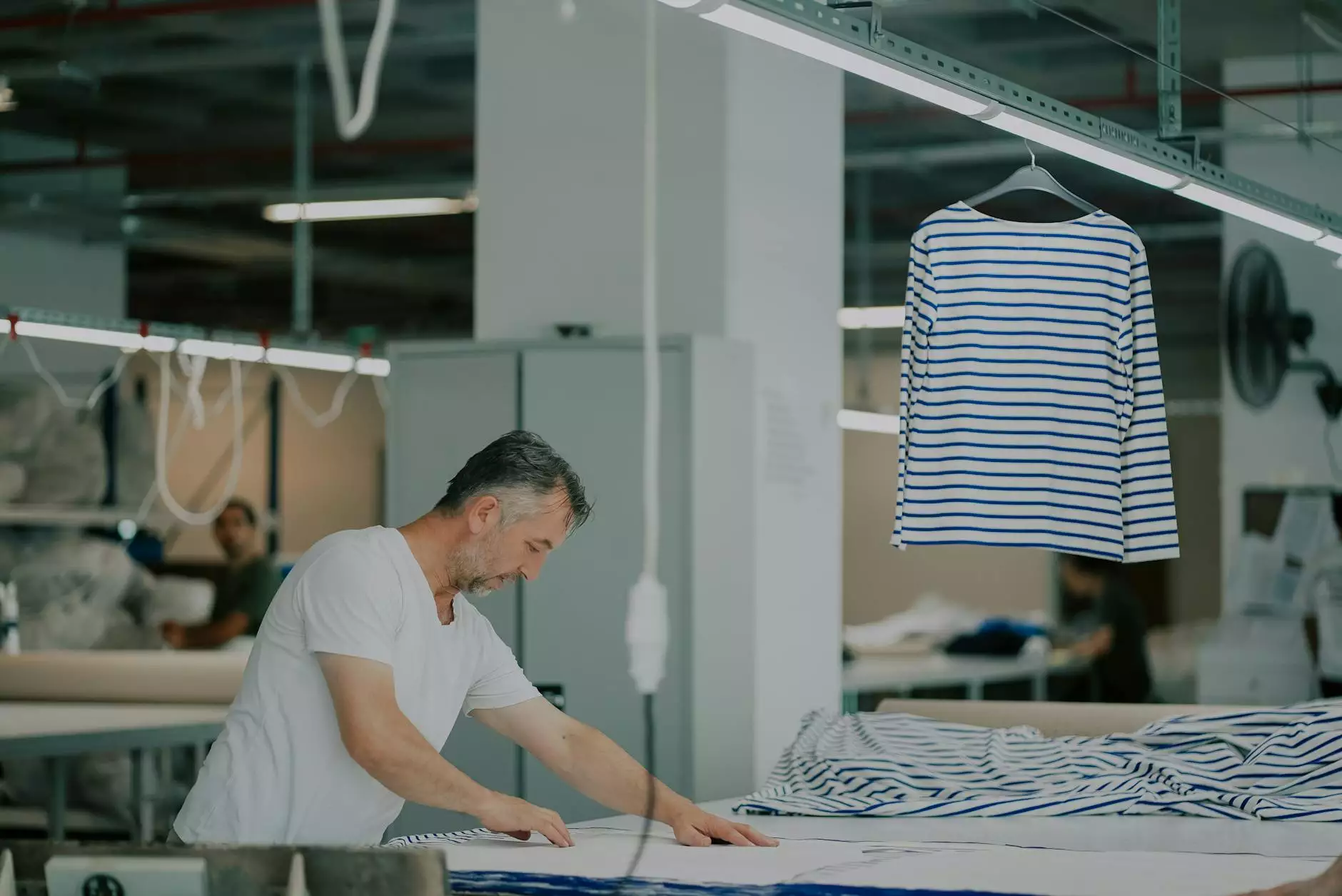
In today's rapidly evolving industrial landscape, the pursuit of precision, efficiency, and innovation is paramount. Companies engaged in metal fabrication and rapid prototyping are at the forefront of this transformation, leveraging cutting-edge techniques and materials to deliver superior products. DeepMould.net, a renowned metal fabricator specializing in diverse industrial solutions, exemplifies this commitment to quality and innovation.
The Crucial Role of Metal Fabricators in Modern Industry
Metal fabricators serve as the backbone of manufacturing, providing essential services that transform raw metal materials into functional, durable components. Their expertise spans several processes, including welding, cutting, bending, and assembling a wide range of metal parts. These skills are vital across sectors such as aerospace, automotive, construction, and consumer electronics.
Key Capabilities of Top-Tier Metal Fabricators
- Precision Cutting and Shaping: Utilizing laser, plasma, or water jet cutting technologies to achieve intricate geometries with minimal material waste.
- Advanced Welding Techniques: Employing TIG, MIG, and spot welding to ensure strong, reliable joints in complex assemblies.
- Bending and Forming: Using hydraulic presses, roll bending, and other forming methods to produce precise curves and structures.
- Surface Treatment: Applying coatings, polishing, and finishing techniques to enhance corrosion resistance and aesthetic appeal.
- Assembly and Integration: Coordinating various metal components into cohesive, high-performance units tailored to client specifications.
Advancements in Metal Fabrication Technologies
The evolution of fabrication techniques has dramatically increased productivity and quality. CNC (Computer Numerical Control) machinery now allows for highly accurate and repeatable operations, while automation and robotics reduce labor costs and improve safety standards. DeepMould.net integrates these innovations to deliver unparalleled results consistently.
The Significance of Rapid Prototype Plastic Parts in Manufacturing
While metal fabrication remains vital, rapid prototype plastic parts have emerged as a game-changer in product development cycles. These prototypes enable designers and engineers to evaluate form, fit, and function before investing in full-scale production. The use of high-quality plastics for rapid prototyping offers numerous benefits, including cost savings, quick turnaround times, and the opportunity for iterative testing.
Why Choose Rapid Prototype Plastic Parts?
- Speed: Rapid prototyping significantly reduces development time, often delivering prototypes within days.
- Cost-Effective: Lower material and production costs compared to traditional manufacturing methods.
- Design Flexibility: Ability to create complex geometries and detailed features that would be challenging with metal or traditional manufacturing.
- Early Function Testing: Validate ergonomic, aesthetic, and functional aspects early in the product development process.
- Iterative Improvement: Quick modifications facilitate continuous refinement and optimization of the design.
Advanced Materials for Rapid Prototype Plastic Parts
The quality of rapid prototype plastic parts hinges on selecting suitable materials. Modern prototypes utilize a wide range of plastics such as ABS, PLA, PETG, nylon, and specialty resins like polypropylene or polycarbonate. These materials are chosen based on properties like tensile strength, flexibility, heat resistance, and chemical durability, aligning with the intended application of the final product.
Key Processes for Manufacturing Rapid Prototype Plastic Parts
Several sophisticated techniques are employed to produce high-fidelity plastic prototypes, each suited for different complexities and volumes:
1. 3D Printing (Additive Manufacturing)
Popular for its versatility and rapid turnaround, 3D printing employs processes like FDM, SLA, SLS, and others to build parts layer by layer with high precision and intricate detail.
2. CNC Machining
Computer-controlled cutting offers excellent surface finish and dimensional accuracy, ideal for prototypes requiring tight tolerances and specific material properties.
3. Resin Casting and Silicone Molds
This method allows for detailed surface finishes and prototypes in multiple iterations, particularly valuable for complex geometries or small production runs.
4. Vacuum Forming and Thermoforming
Suitable for creating large, hollow, or thin-walled prototypes quickly and cost-effectively, especially when testing product enclosures or packaging.
Integrating Metal Fabrication with Plastic Prototyping for Comprehensive Product Development
Modern manufacturing often combines metal fabrication and rapid prototype plastic parts to optimize the product development cycle. For example, initial concept models in plastic can undergo ergonomic testing, while metal prototypes can be used for durability and performance validation. This integrated approach allows companies to rapidly iterate designs, reduce time-to-market, and enhance product quality.
DeepMould.net: Your Partner in Metal Fabrication and Rapid Prototyping
As a leading metal fabricator, DeepMould.net specializes in delivering precision-engineered metal components tailored to meet diverse industrial needs. With state-of-the-art equipment and a team of experienced engineers, they ensure every project adheres to the highest standards of quality and accuracy.
Moreover, DeepMould.net offers advanced rapid prototype plastic parts solutions, employing the latest additive manufacturing techniques. This enables customers to speed up their product development timelines, reduce costs, and improve overall design quality.
The Advantages of Partnering with DeepMould.net
- Comprehensive Solutions: From metal fabrication to rapid prototyping, covering all your manufacturing needs under one roof.
- Quality Assurance: Rigorous testing and quality control processes ensure reliable, high-performance parts.
- Customization: Tailored services to meet specific project requirements and industry standards.
- Fast Turnaround: Efficient workflows to minimize lead times without compromising quality.
- Technical Expertise: Skilled professionals guiding your project from concept to production.
How to Maximize the Benefits of Metal Fabrication and Rapid Prototyping
For businesses looking to harness the full potential of metal fabrication and rapid prototyping, consider the following strategies:
- Early Collaboration: Engage with your manufacturing partner during the initial design phase to identify opportunities for optimization.
- Material Selection: Choose appropriate metals and plastics based on the intended use, durability requirements, and environmental factors.
- Prototype Testing: Utilize rapid prototypes to evaluate ergonomic, aesthetic, and functional aspects before committing to production.
- Iterative Design: Leverage quick turnaround times to refine designs continuously, ensuring the final product exceeds expectations.
- Cost Analysis: Balance between material costs, manufacturing processes, and project timelines to optimize overall budget.
Future Trends in Metal Fabrication and Rapid Prototyping
The manufacturing industry is poised for exciting innovations that will further enhance capabilities:
- Industrial 4.0 Integration: Smart factories utilizing IoT, AI, and data analytics for real-time process optimization.
- Emergence of Advanced Materials: Development of new alloys and plastics with superior properties for specialized applications.
- Hybrid Manufacturing: Combining additive and subtractive methods to achieve complex geometries with superior surface finishes.
- Sustainable Manufacturing: Emphasizing eco-friendly processes and recyclable raw materials to reduce environmental impact.
Conclusion: Embracing Innovation for Competitive Success
In summary, the synergy between metal fabricators and the capabilities of rapid prototype plastic parts plays a crucial role in modern manufacturing. Embracing these technologies enables companies to accelerate product development, improve quality, and maintain a competitive edge. DeepMould.net stands ready to be your trusted partner, delivering precision, innovation, and excellence across all your manufacturing projects.
Investing in advanced fabrication and prototyping solutions today paves the way for more efficient, innovative, and sustainable manufacturing practices tomorrow. Whether you are developing prototypes for new products or producing high-volume metal components, the strategic integration of these technologies will accelerate your success in a highly competitive global market.