Injection Mold Tool Design: A Comprehensive Guide
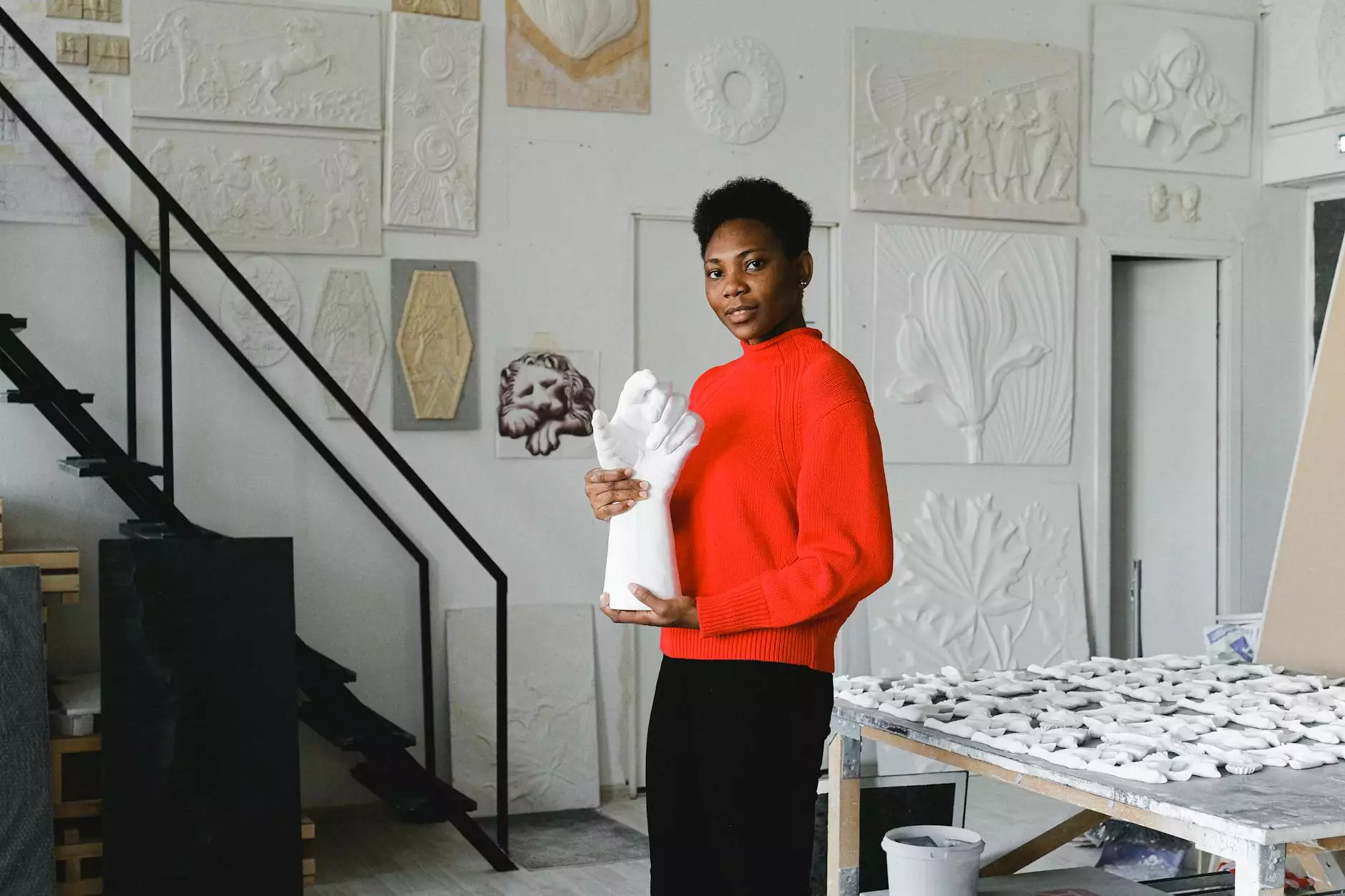
In the world of manufacturing, injection mold tool design stands as a cornerstone of production efficiency and innovation. For metal fabricators, understanding the nuances of this design process is vital for delivering high-quality products consistently and competitively. This article aims to provide an exhaustive overview of injection mold tool design, including its importance, processes, materials, and best practices.
Understanding Injection Mold Tool Design
Injection mold tool design is the systematic process of creating molds used for shaping materials, often thermoplastics and metals, into precise parts or products. The process involves several critical steps, each contributing to the overall success of the manufacturing operation. Let's take a deeper look into what this entails:
The Importance of Mold Tool Design
The significance of mold tool design cannot be overstated. Here are several key reasons why it matters:
- Precision Engineering: Proper mold design ensures that the final products are manufactured with high accuracy, vital for industries such as automotive and aerospace.
- Cost Efficiency: A well-designed mold reduces material waste and manufacturing time, enhancing overall productivity.
- Product Quality: The integrity and durability of the end product are significantly influenced by the quality of the mold.
- Flexibility: Modern designs allow for the production of complex geometries and features, which expand product capabilities.
The Process of Designing Injection Molds
The injection mold tool design process involves various stages that require expertise in engineering and an understanding of material properties. Below is a detailed breakdown of these stages:
1. Concept Development
The first step in injection mold tool design is the development of a concept based on product requirements. This includes:
- Understanding customer specifications and applications
- Evaluating design constraints and requirements
- Creating initial sketches and design ideas
2. 3D Modeling
Once a concept is established, designers use 3D modeling software like SolidWorks or Autodesk Inventor to create detailed digital representations of the mold. This phase involves:
- Designing the geometry of the mold
- Incorporating features such as ejector pins and cooling channels
- Simulating the injection process to identify potential issues
3. Material Selection
Choosing the right materials for mold construction is crucial. Designers typically consider:
- Steel: Known for its durability and strength, it's often used for high-production molds.
- Aluminum: Lightweight and cost-effective, suitable for lower-volume runs.
- Temperature-Resistant Alloys: Important for maintaining performance in high-heat applications.
4. Prototyping
After finalizing the design, a prototype of the mold is often created. This allows for testing and validation. Key benefits include:
- Early detection of design flaws
- Improved adjustments before full-scale production
- Cost-saving through reduced revisions
5. Finalizing the Design
Upon successful prototyping and testing, designers finalize the mold design, preparing it for production. This step includes:
- Incorporating feedback from testing
- Optimizing designs for manufacturing and assembly
- Preparing design documentation and specifications
Challenges in Injection Mold Tool Design
Despite its advantages, injection mold tool design faces several challenges that can affect production. Being aware of these challenges is vital for metal fabricators:
1. Complexity of Designs
As products become more intricate, the molds must also evolve. This complexity can lead to:
- Increased manufacturing costs
- Longer lead times
- A higher likelihood of defects if not managed properly
2. Material Limitations
Understanding the properties of different materials is critical. Choosing an inappropriate material can result in:
- Reduced mold lifespan
- Compromised product quality
- Increased maintenance requirements
3. Production Variances
Variability in production processes can lead to inconsistent product outcomes. Addressing this challenge involves:
- Implementing strict quality control
- Utilizing advanced technologies for monitoring production
Trends in Injection Mold Tool Design
The industry of injection mold tool design continuously evolves. Staying updated on current trends allows metal fabricators to stay competitive. Here are notable trends shaping the future:
1. Advanced Materials
The introduction of new materials enhances mold characteristics, such as:
- Better heat resistance
- Increased lifespan and reduced maintenance
2. Automation and AI Integration
Embracing automation and AI in design and production can lead to more efficient processes, allowing for:
- Real-time data analysis for decision-making
- Enhanced precision in mold creation
3. Sustainable Practices
With a heightened focus on sustainability, many companies are adopting eco-friendly practices, such as:
- Minimizing waste through efficient design
- Utilizing recyclable materials and processes
Best Practices for Successful Mold Tool Design
For metal fabricators aiming to excel in injection mold tool design, adhering to best practices is essential. Here’s a list of recommendations:
1. Collaborate Early with Stakeholders
Involving engineers, designers, and production staff during the initial design phase promotes a comprehensive approach, ensuring:
- All considerations are accounted for from the outset
- Enhanced buy-in from various teams, fostering smoother production
2. Invest in Advanced Software
Utilizing the latest software tools for design and simulation can predict issues before they arise, enabling:
- More streamlined workflows
- Time and cost savings in the production process
3. Continuous Training and Development
Keeping design teams updated with the latest trends and technologies ensures the incorporation of best practices, leading to:
- Innovation in designs
- Staying ahead in the competitive landscape
Conclusion
In conclusion, injection mold tool design holds paramount importance in the manufacturing sector, particularly for metal fabricators striving for excellence. By understanding the complexities, embracing advanced practices, and keeping pace with trends, businesses can ensure high-quality outcomes and robust production processes. As we move forward, continuous learning and adaptation will be key to a thriving manufacturing future.
For metal fabricators seeking reliable partners in their injection mold tool design journey, visiting deepmould.net can provide insights into achieving precision and efficiency in their projects.